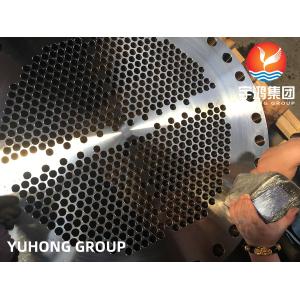
Add to Cart
ASME SA182 F316L TUBESHEET For Floating Head Exchanger Shell Heat Exchanger
A tube sheet is an essential component of a heat exchanger. It is a circular plate that contains a series of holes to hold the tubes in place. The tubes are inserted through these holes and then expanded or welded to the tube sheet to create a strong and leak-tight connection.
The tube sheet acts as a barrier between the high-pressure and low-pressure sides of the heat exchanger. It ensures that the fluids flowing through the tubes do not mix with each other. The tube sheet also provides support and stability to the tubes, preventing them from sagging or vibrating under operating conditions.
Tube sheets are typically made of materials that can withstand high temperatures and corrosive environments, such as stainless steel, carbon steel, or titanium. The material selection depends on the specific requirements of the heat exchanger, including the type of fluids being processed and the operating conditions.
The design of the tube sheet is crucial for efficient heat transfer and to prevent tube failure. Factors such as the diameter and thickness of the tubes, the pitch (spacing) between the tubes, and the number and arrangement of the holes in the tube sheet are carefully considered during the design process.
In addition to holding the tubes in place, tube sheets also provide a surface for attaching the shell or housing of the heat exchanger. The shell is typically bolted or welded to the tube sheet to create a sealed enclosure for the tubes.
The tube sheet plays a vital role in the performance and reliability of a heat exchanger. It ensures proper fluid separation, supports the tubes, and provides a secure connection between the tubes and the shell.
Chemical Compostion and Properties
Grade | C | Mn | Si | P | S | Cr | Mo | Ni | N | |
316 | Min | - | - | - | 0 | - | 16.0 | 2.00 | 10.0 | - |
Max | 0.08 | 2.0 | 0.75 | 0.045 | 0.03 | 18.0 | 3.00 | 14.0 | 0.10 | |
316L | Min | - | - | - | - | - | 16.0 | 2.00 | 10.0 | - |
Max | 0.03 | 2.0 | 0.75 | 0.045 | 0.03 | 18.0 | 3.00 | 14.0 | 0.10 | |
316H | Min | 0.04 | 0.04 | 0 | - | - | 16.0 | 2.00 | 10.0 | - |
max | 0.10 | 0.10 | 0.75 | 0.045 | 0.03 | 18.0 | 3.00 | 14.0 |
|
Grade | Tensile Str (MPa) min | Yield Str 0.2% Proof (MPa) min | Elong (% in 50mm) min | Hardness | |
Rockwell B (HR B) max | Brinell (HB) max | ||||
316 | 515 | 205 | 40 | 95 | 217 |
316L | 485 | 170 | 40 | 95 | 217 |
316H | 515 | 205 | 40 | 95 | 217 |
Grade | Density (kg/m3) | Elastic Modulus (GPa) | Mean Co-eff of Thermal Expansion (µm/m/°C) | Thermal Conductivity (W/m.K) | Specific Heat 0-100°C (J/kg.K) | Elec Resistivity (nΩ.m) | |||
0-100°C | 0-315°C | 0-538°C | At 100°C | At 500°C | |||||
316/L/H | 8000 | 193 | 15.9 | 16.2 | 17.5 | 16.3 | 21.5 | 500 | 740 |
APPLICATIONS :
1. petrochemical industry
2. Pharmaceutical industry
3. Food industry
4. Aviation and aerospace industry
5. Architectural decoration industry
6. Oil and gas industry
7. Heat Exchanger Parts