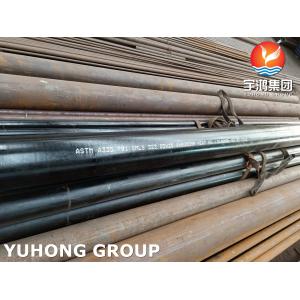
Add to Cart
ASTM A335 / ASME SA335 P91 Alloy Steel Seamless Pipe for High-Temperature Service
ASTM A335/SA335 P91 is a ferritic alloy steel that has very high strength properties, which do not deteriorate with time, and are creep resistant. It is also called 9 Cr 1 Mo steel, or chrome moly pipe, based on its composition. Alloy P91 pipe is primarily composed of chromium (Cr), molybdenum (Mo), and vanadium (V) as key alloying elements. The specific composition of P91 typically includes around 9% chromium and 1% molybdenum, in addition to other elements like carbon, manganese, silicon, and nitrogen. Other alloy grades may have different compositions tailored for specific applications.
Main Materials
ASTM A335 (Seamless Ferritic Alloy-Steel Pipe for High-Temperature Service)
ASTM A335 P1, P2, P5, P9, P12, P11, P22, P91
ASTM 213(Seamless Ferritic and Austenitic Alloy-Steel Boiler, Superheater, and Heat-Exchanger Tubes)
ASTM A213 T1, T2, T11, T5, T9, T22, T23, T91, T92
A335 Grade P91 Pipe Equivalent Material
ASTM | ASME | Equivalent material |
---|---|---|
A335 P 91 | ASME SA 335 P91 | 1.4903, K90901, X10CrMoVNb9-1 |
A335 Grade P91 Pipe Equivalent Material Chemical Requirements
Element | Grade | P-5 | P-9 | P-11 | P-22 | P-91 | P-91 shall also include the following: |
---|---|---|---|---|---|---|---|
UNS Designation | K41545 | S50400 | K11597 | K21590 | K91560 | ||
Carbon | 0.15 max | 0.15 max | 0.05 – 0.15 | 0.05 – 0.15 | 0.08 – 0.12 | V at 0.18 – 0.25 | |
Manganese | 0.30 – 0.60 | 0.30 – 0.60 | 0.30 – 0.60 | 0.30 – 0.60 | 0.30 – 0.60 | N at 0.030 – 0.070 | |
Phosphorous, max | 0.025 | 0.025 | 0.025 | 0.025 | 0.020 | Ni at 0.40 max | |
Sulfur, max | 0.025 | 0.025 | 0.025 | 0.025 | 0.010 | Al at 0.02 max | |
Silicon | 0.50 max | 0.25 – 1.00 | 0.50 – 1.00 | 0.50 max | 0.20 -0.50 | Cb at 0.06 – 0.10 | |
Chromium | 4.00 – 6.00 | 8.00 – 10.00 | 1.00 – 1.50 | 1.90 – 2.60 | 8.00 – 9.50 | Ti at 0.01 max | |
Molybdenum | 0.45 -0.65 | 0.90 – 1.10 | 0.44 – 0.65 | 0.87 – 1.13 | 0.85 – 1.05 | Zr at 0.01 max |
Mechanical Properties | ||||||
Grade | Tensile strength(MPa) | Yield strength(MPa) | Elongation(%) | Impact energy(J) | Hardness | |
P11 | ≥ 415 | ≥ 205 | ≥ 22 | ≥ 35 | ≤ 163HB | |
P12 | ≥ 415 | ≥ 220 | ≥ 22 | ≥ 35 | ≤ 163HB | |
P22 | ≥ 415 | ≥ 205 | ≥ 22 | ≥ 35 | ≤ 163HB | |
P5 | ≥ 415 | ≥ 205 | ≥ 22 | ≥ 35 | ≤ 187HB | |
P91 | 585~760 | ≥ 415 | ≥ 20 | ≥ 35 | ≤ 250HB | |
P92 | ≥ 620 | ≥ 440 | ≥ 20 | ≥ 35 | 250HB |
The difference between alloy P91 pipe and other alloy grades commonly used in the industry:
Alloy Composition: Alloy P91 pipe is primarily composed of chromium (Cr), molybdenum (Mo), and vanadium (V) as key alloying elements. The specific composition of P91 typically includes around 9% chromium and 1% molybdenum, in addition to other elements like carbon, manganese, silicon, and nitrogen. Other alloy grades may have different compositions tailored for specific applications.
High-Temperature Strength: One of the main differentiating factors of P91 is its exceptional strength at elevated temperatures. It offers superior creep strength and resistance to thermal fatigue compared to many other alloy grades. This makes it suitable for high-temperature applications in power plants, boilers, and petrochemical industries.
Carbon Content: P91 has a higher carbon content compared to some other alloy grades, which contributes to its increased strength and hardness. However, this higher carbon content also leads to challenges during welding, requiring precise control of heat input and post-weld heat treatment.
Fabrication and Weldability: Alloy P91 has specific requirements when it comes to fabrication and welding. It necessitates precise preheating, interpass temperature control, and post-weld heat treatment to avoid detrimental effects on the material's microstructure and properties. Other alloy grades may have different welding procedures and considerations.
Application
A335/SA335 P91 is suitable for bending, flanging (vanstoning), and similar forming operations and for fusion welding. Its commonly used in below usages.
Power Generation
Oil and Gas Industry
Chemical Processing
Industrial Boilers
Heat Exchangers